Buckle Up: Understanding Fastener Safety Standards That Keep Us Together
11/18/2024
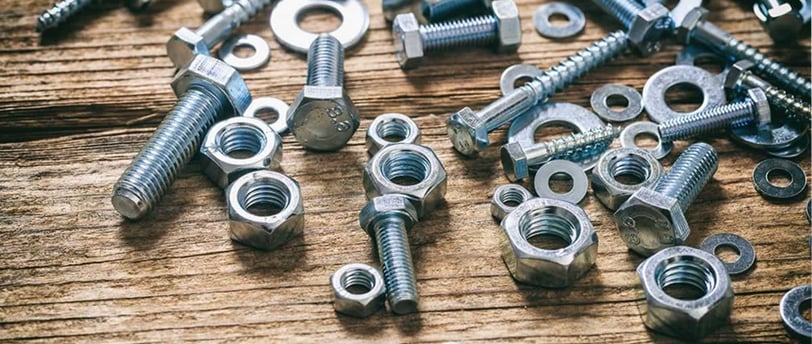
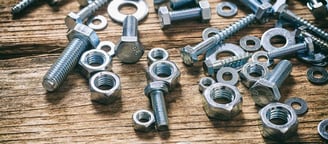
The Importance of Fastener Safety Standards
In the world of construction and manufacturing, fasteners are the unsung heroes that hold everything together. However, with great power comes great responsibility, and that's where fastener safety standards come into play. These standards ensure that fasteners, such as bolts, screws, and nuts, meet safety and performance requirements—ultimately preventing catastrophic failures that could lead to accidents or injuries.
Key Industry Standards for Fastener Quality
Various organizations set forth guidelines to enforce safety and quality in the fastener industry. Most notable among them is the International Organization for Standardization (ISO), the American National Standards Institute (ANSI), and the Automotive Industry Action Group (AIAG). Each organization has established specific testing and certification protocols to ensure that fasteners can bear the loads they are designed for.
For instance, ISO 898-1 specifies the mechanical properties of fasteners made of carbon steel and alloy steel, allowing manufacturers and customers to check that the fasteners meet the necessary criteria. Furthermore, ANSI/ASME standards ensure that commercially available fasteners conform to established safety and quality norms, helping to prevent unexpected failures.
Effective Quality Testing Methods
Quality testing in the fastener industry is not just a ‘nice-to-have’; it’s a must to ensure dependability. There are several testing methods that companies should employ, including tensile testing, impact testing, and fatigue testing.
Tensile testing evaluates the strength and ductility of fasteners, helping to identify how they will behave under tension. Impact testing determines their resistance to sudden force or shock, while fatigue testing assesses how they will perform under cyclic loading. By using these testing methods regularly, manufacturers can ensure that their fasteners are up to the task of holding it all together, literally!
Moreover, it's crucial that companies invest in well-equipped laboratories and trained personnel to conduct these tests. Remember, various national and regional standards may require specific certifications for fasteners, so staying compliant is key in avoiding unexpected liabilities. Quality fasteners not only ensure safety but also enhance the overall integrity of the structures they support.
Ensuring Fastener Safety and Compliance
So, how can manufacturers ensure fastener safety and compliance with industry standards? First and foremost, it’s essential to stay updated on the latest safety regulations and changes within the industry. Many organizations provide resources and workshops to help stakeholders understand new requirements.
Next, establishing a robust quality control system that includes regular inspections and audits will dramatically improve fastener safety compliance. Training employees to recognize the significance of quality and safety centered on fasteners will go a long way toward embedding a culture of safety within the company.
Lastly, consider engaging a third-party inspection service for unbiased evaluation of your products. Not only will this promote diligence in maintaining fastener safety, but it could also improve customer confidence in your brand. After all, it’s about helping hold the world together—safely!