The Impact of Station Quantity in Cold Formers on Fastener Production
12/13/20244 min read
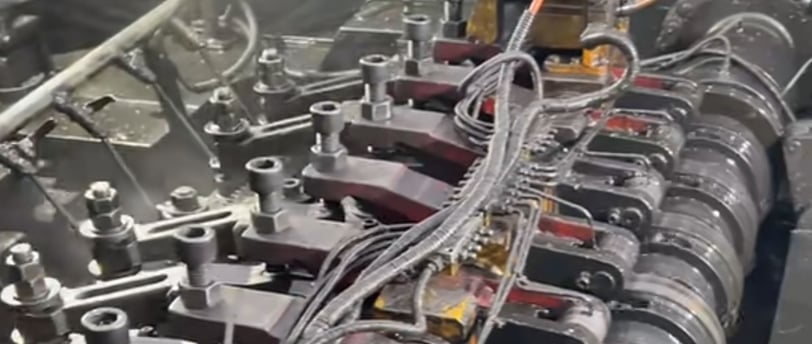
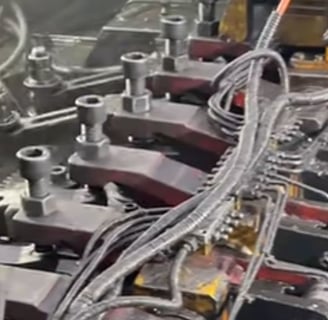
Understanding Cold Formers
Cold forming technology plays a pivotal role in the fastener production industry, allowing manufacturers to create high-quality, precise metal components through a series of deformation processes without the need for heating. This technique enhances material efficiency and typically results in stronger products due to the work hardening of metals. At the heart of this technology lies the cold former, a specialized machine designed to shape and form metal wire or strips into fasteners.
A cold former comprises critical components, including a feed mechanism, a forming die, and a control system. The feed mechanism guides the material into the die, where it is shaped through a sequence of punches and dies. The configuration of these components, particularly the number of stations within the cold former, significantly impacts the manufacturing process. Common configurations include three, four, five, and six-station systems, each enabling different forming capabilities and efficiencies.
The number of stations in a cold former directly influences the complexity and variety of fasteners that can be produced in a single cycle. For example, a three-station system may be suitable for simpler fasteners or lower production volumes. In contrast, a six-station system can handle more intricate designs and higher output demands. Each additional station allows for extra operations to be performed, such as blanking, forming, and trimming, thereby improving productivity and reducing cycle times.
Moreover, the configuration of the cold former not only affects the speed and efficiency of production but also the overall quality and consistency of the fasteners produced. As manufacturers seek to optimize their production processes, selecting the appropriate cold former configuration becomes essential in ensuring that they meet the demands of the fastener market while maintaining operational efficiency.
Production Efficiency with Varying Number of Stations
The relationship between the number of stations in cold formers and the efficiency of fastener production is a crucial aspect that affects the overall output and product quality. In cold forming, each station is responsible for a specific operation, sequentially shaping the raw material into the desired fastener. By increasing the number of stations, manufacturers can significantly enhance the efficiency of the production process.
For instance, a three-station cold former can accommodate basic operations, making it suitable for simpler fastener designs. However, it may require additional setups or manual interventions to complete more complex parts, leading to increased cycle times and potential bottlenecks. In contrast, a six-station cold former offers the advantage of simultaneous operations, allowing multiple shaping processes to take place without interruption. This can lead to a significant reduction in downtime and an improvement in overall output rates, as the machine can produce more parts within the same time frame.
Furthermore, optimizing material usage becomes more feasible with a greater number of stations. Advanced cold formers can effectively manage material flow and minimize scrap, contributing to cost savings and enhanced sustainability. However, the complexities of operating a six-station system may result in higher maintenance requirements and initial investment costs. Manufacturers must therefore carefully assess their production demands and capabilities when choosing between three-station and six-station cold formers, weighing the benefits of higher output against the potential increase in operational complexity.
In conclusion, the choice of the number of stations in cold formers is a vital decision for optimizing production efficiency within the fastener industry. By evaluating the trade-offs between cycle times, output rates, and maintenance needs, manufacturers can align their equipment configuration with their production goals and market demands.
Customization and Versatility of Stations
The number of stations in cold formers significantly influences the ability to produce customized or non-standard fasteners. Cold forming machines, particularly those equipped with six stations, provide enhanced capabilities compared to their three or four-station counterparts. This aspect of cold forming is crucial for industries that demand intricate designs and specifications, as it ultimately determines the variety of fasteners that can be produced.
The versatility of a cold former is paramount, especially when manufacturers aim to address specific customer requirements. For instance, a six-station cold former can undertake complex sequences of operations that involve multiple forming steps, allowing for the creation of uniquely shaped fasteners in a single production cycle. This includes the ability to produce various head shapes, lengths, and diameters, which is a notable advantage for manufacturers looking to streamline their production lines.
Additionally, custom fasteners often require specific tolerances and finishes that can only be achieved with more advanced setups. A case in point can be seen in the automotive industry, where fasteners may need to meet stringent performance and safety standards. By employing a six-station cold former, manufacturers can efficiently create fasteners that not only meet these standards but also allow for further customization, such as unique coatings or surface treatments that enhance durability.
Moreover, the flexibility of these machines can lead to reduced setup times when switching between different fastener types. This adaptability is particularly beneficial in a market where demand can change rapidly, as it enables manufacturers to respond efficiently without incurring significant downtime. Ultimately, the choice of the number of stations in a cold former plays a critical role in determining the production capabilities for customized fasteners, impacting overall efficiency and market competitiveness.
Key Considerations When Choosing a Cold Former
The selection of a cold former is a critical decision for manufacturers involved in fastener production. One of the primary factors to consider is the number of stations in the machine, which directly impacts the production volume capabilities. Machines with more stations typically allow for greater flexibility and increased output. This is particularly crucial for manufacturers aiming to meet high production volume requirements while maintaining consistent quality in their fastener products. Evaluating the expected output per hour and aligning it with the capacity of the cold former becomes essential in this context.
Another significant factor is the product specifications. Fasteners come in various shapes and sizes, each requiring specific tooling and setup. Understanding the product range that the operation intends to produce is vital when selecting a cold former. Some machines are better suited for complex shapes and tight tolerances, while others may excel in producing simple designs efficiently. The choice should, therefore, reflect the specific needs of the production line.
Budget constraints also play a pivotal role in the selection process. Cold formers can vary significantly in price based on the number of stations and their technological capabilities. It is crucial for manufacturers to assess their financial resources and determine a balance between investment and expected returns. While higher initial costs may be associated with more advanced machines, they might also offer better long-term efficiency, which can justify the expenditure.
Finally, operational capabilities, including the skillset of the workforce and maintenance availability, need thorough consideration. The introduction of advanced cold forming technologies may require specialized training for operators to maximize the potential of the machines. Future trends in fastener production technology—such as automation and Industry 4.0—should inform decisions about cold former setups, ensuring longevity and adaptability in an evolving market.