Fastener Selection: The Secret Sauce to Your Bolted Success!
xijifastener
10/28/2024
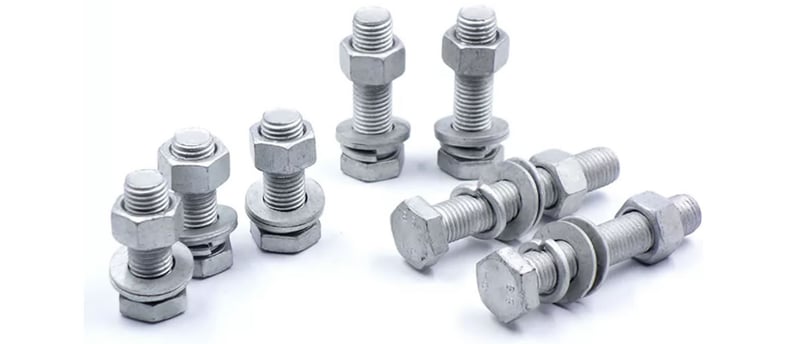
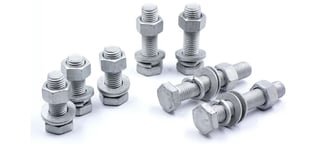
Understanding Fasteners: The Basics You Need to Know
Fasteners are essential components in a multitude of applications, providing the means to join two or more objects together securely. These vital elements prevent disassembly under various conditions, ensuring that structures maintain their integrity over time. In simple terms, without fasteners, assembling furniture could quickly devolve into an exercise in frustration, akin to trying to hold an unruly puzzle together without glue.
Among the myriad types of fasteners, screws, bolts, nuts, and washers are the most commonly encountered. Screws are threaded fasteners that are typically inserted into pre-drilled holes; their helical ridges aid in securing materials. Bolts, on the other hand, are wider and mainly require a nut to facilitate a secure hold, acting much like a sturdy handshake between two components. Nuts, which are hexagonal in shape, are used in conjunction with bolts to create a tight joint, while washers serve to distribute the load and protect surfaces from damage, much like a good cushion prevents a hard impact.
The proper selection of fasteners is paramount not only for structural integrity but also for safety and efficiency in any application. Each fastener comes with unique specifications, including load capacity, material compatibility, and corrosion resistance. Choosing the wrong type can lead to failures that might cause delays, increase costs, or, in the worst cases, result in structural failures. Understanding the nuances of different fasteners is akin to a chef selecting the right spices for a dish—each ingredient has a purpose, and the final outcome is only as good as the components used.
In essence, fasteners are the unsung heroes of construction and assembly, quietly holding our world together. Grasping the fundamentals of fasteners is essential for anyone engaged in design or assembly tasks, ensuring that projects are completed successfully and safely.
Material Matters: Choosing the Right Fastener Material
When it comes to fastener selection, the material from which a fastener is made plays a pivotal role in determining its performance and durability. The most common materials used for fasteners include stainless steel, carbon steel, brass, and plastic, each offering unique properties that suit different applications.
Stainless steel is known for its exceptional corrosion resistance, making it an ideal choice for fasteners exposed to harsh environments, such as outdoor or marine applications. Its strength-to-weight ratio is advantageous, allowing for secure closures without adding excessive weight. However, in extreme temperature conditions, it can lose some of its structural integrity.
On the other hand, carbon steel is favored for its high strength and cost-effectiveness. It is a great option for applications that do not require corrosion resistance, as it can rust if not properly treated. When considering fastener materials, one should assess the environment in which the fasteners will operate. A poorly chosen carbon steel bolt in a damp location could lead to failure due to corrosion, not to mention the potential project delays and financial repercussions that could ensue.
Brass, with its attractive appearance and excellent corrosion resistance, is often used in decorative applications. It is softer than stainless and carbon steel, which means it may not be suitable for high-stress environments. Conversely, plastic fasteners are lightweight and resistant to corrosion, making them suitable for electrical applications or environments where metal fasteners could cause undesirable electrical interference.
Ultimately, selecting the appropriate fastener material requires an understanding of the specific application and environmental conditions. For instance, using stainless steel fasteners in a coastal setting mitigates corrosion risks, whereas carbon steel might be more suitable in an indoor setting. Therefore, proper material choice is crucial to avoid undesirable consequences and ensure the long-term success of your bolted assembly.
Specifications That Matter: Sizes and Grades Explained
Fastener specifications, particularly sizes and grades, play a pivotal role in ensuring the performance and safety of bolted connections. Understanding elements such as thread types, lengths, and grades is essential for any engineer or DIY enthusiast looking to achieve reliable outcomes. Fasteners come in various sizes, and the correct choice depends on the specific application; using the wrong size can lead to inadequate clamping force, resulting in joint failure. Thread types, including coarse and fine, also significantly impact how a fastener performs. Coarse threads, for example, are ideal for high-torque applications, while fine threads offer better tension control.
Grades are another crucial specification that defines a fastener's material strength, yielding, and tensile requirements. Standards set forth by organizations such as ASTM (American Society for Testing and Materials), ISO (International Organization for Standardization), and SAE (Society of Automotive Engineers) provide important guidelines that manufacturers must adhere to. Knowing a fastener's grade can help in selecting the most suitable fastener for environments subjected to vibrations, extreme temperatures, or corrosive conditions.
One amusing hypothetical scenario illustrating the significance of correct specifications might involve a DIYer choosing an M6 bolt for a crucial component in a racing vehicle by mistake, believing it would hold well due to its generic appearance. The next moment, on the test track, the improperly chosen fastener fails at high speed, leading to a comical yet hazardous outcome. Such mishaps underline the necessity of meticulous selection to prevent accidents and ensure functionality.
Ultimately, prioritizing the right sizes and grades in fastener selection fosters bolted success. Proper awareness of specifications promotes not only performance but also safety, as miscalculated choices can lead to potentially catastrophic results. By understanding these fundamentals, individuals can navigate their fastener needs more effectively, enhancing their engineering or construction projects.
Application Scenarios: Matching Fasteners to Projects
Selecting the right fasteners for specific applications is a crucial step in ensuring the durability and efficiency of a project. Different industries have unique demands and environmental conditions that dictate the choice of fasteners. Understanding these distinctions can significantly enhance the quality of work across various fields such as construction, automotive, electronics, and aerospace.
In the construction industry, for instance, fasteners must withstand immense physical stress and environmental elements. Options such as galvanized bolts and stainless-steel screws offer the required durability against rust and corrosion. In contrast, the automotive sector often leverages specialized fasteners, like high-strength bolts, designed to endure extreme vibrations and temperature fluctuations. Choosing the right fastener can reduce the risk of component failure, ensuring safety and performance in vehicles.
Electronics projects, which often involve intricate assemblies, require precision fasteners such as micro screws or snap fittings, which allow for minimal intrusion and maintain the integrity of delicate components. Fasteners used in this industry must also be non-magnetic and non-corrosive to prevent interference with electronic signals and degradation over time. Aerospace, on the other hand, employs fasteners made from aerospace-grade aluminum or titanium, known for their lightweight yet robust properties to handle extreme conditions in flight.
To assist with choosing fasteners for your projects, consider utilizing a checklist that assesses the material needs, environmental exposure, and stress factors pertinent to your specific application. Additionally, reviewing individual project requirements against standard fastener specifications can lead to insightful decisions. As you embark on this fastener selection journey, embrace it with confidence; after all, even fasteners deserve thoughtful consideration to avoid any 'screw-ups'!